G-Camp field experience has built a dedicated following
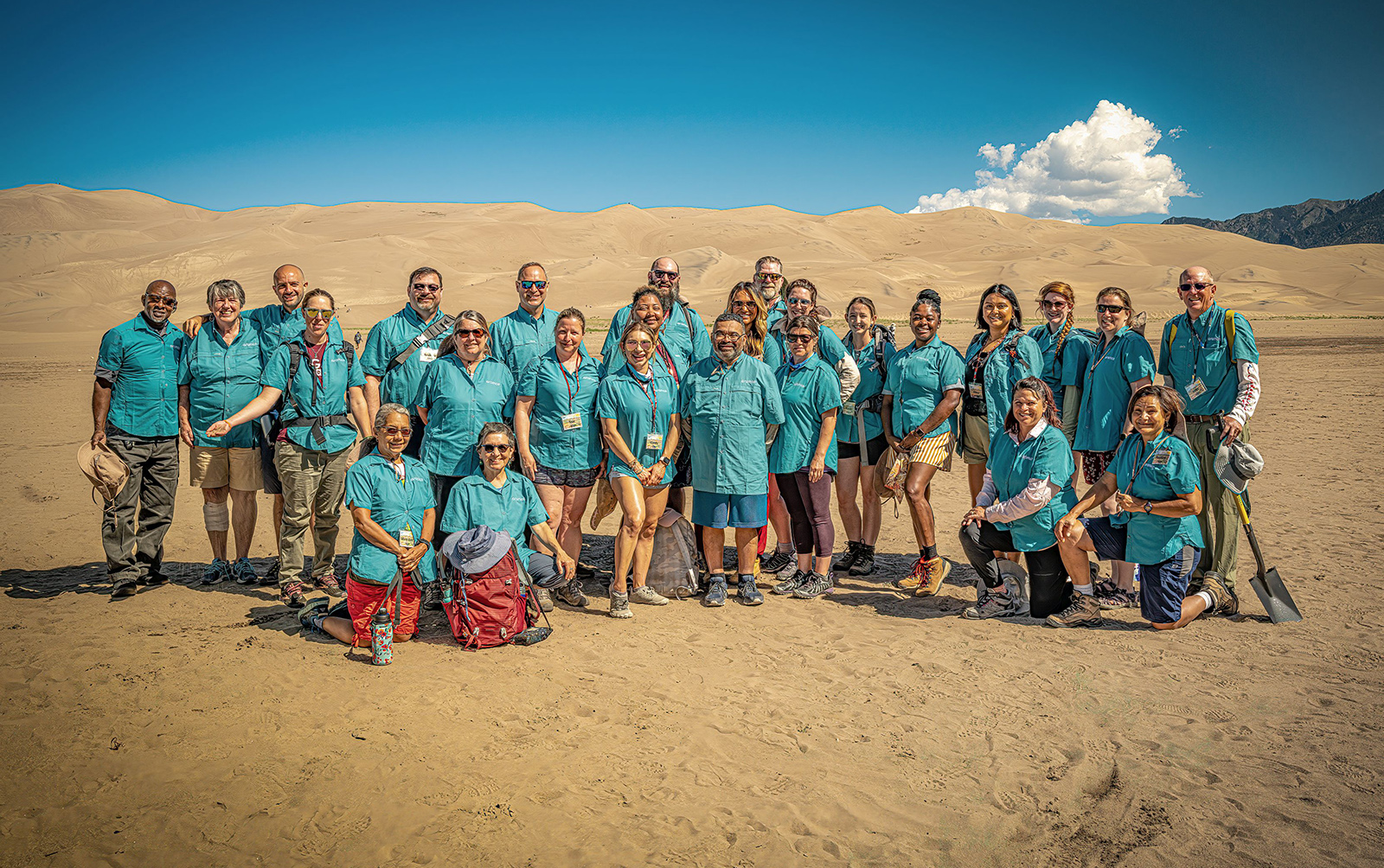
Texas A&M University hosts an annual geology camp, known as G-Camp, as a way to invest in professional development for science teachers to enrich the classroom experience for their students.
Texas A&M University hosts an annual geology camp, known as G-Camp, as a way to invest in professional development for science teachers to enrich the classroom experience for their students.
The program was founded in 2007 and Aramco Americas has been a sponsor for more than a decade. Teachers from around the U.S. apply to participate in this once in a lifetime experience.
This year Andrew Silver, geological specialist & data scientist, Aramco Americas Upstream, participated in the camp supporting Texas A&M professors by delivering lessons, mentoring field studies, and connecting the relevance of academic learnings to real-world business and social impacts.
Sites in Texas, Colorado, and New Mexico were visited to experience and see first-hand various geologic processes and a variety of rock formations including sedimentary, such as marine and coastal, as well as volcanic, and metamorphic outcrops. In addition, the teachers visited an underground gold/silver mine and learned how to sample and monitor surface water in streams.
“G-Camp teachers influence tens of thousands of students each year, inspiring many of them to enter STEM careers," said Silver. "Some may even be future geoscientists and provide the high-quality talent needed as our industry moves forward."
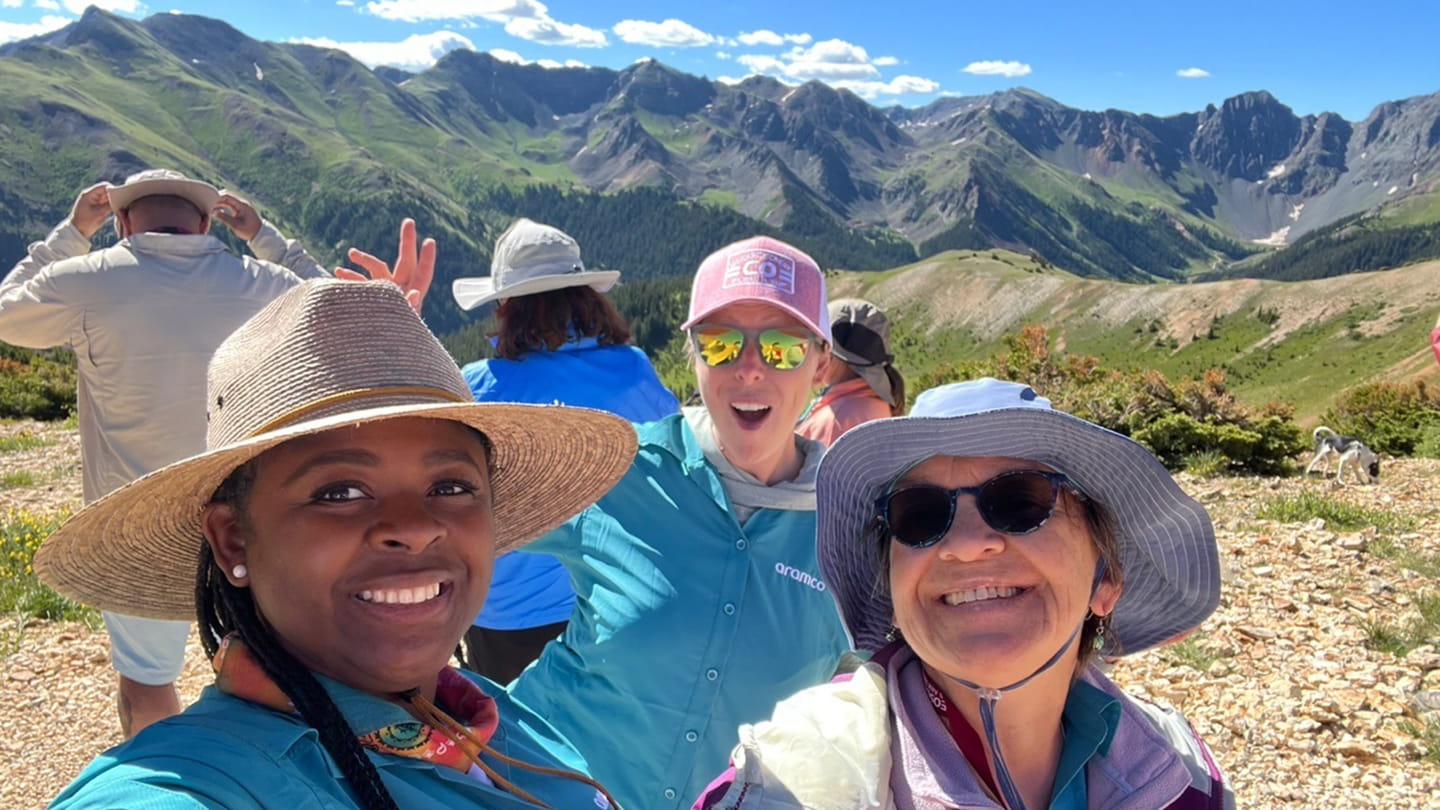
This year’s G-Camp class included 20 middle and high school science teachers from 11 states across the U.S. What has been so amazing is the multiplier effect of this program and its popularity with teachers and alumni alike has resulted in the creation of an active online social media community of G-Camp attendees through Facebook.
This year’s G-Camp class included 20 middle and high school science teachers from 11 states across the U.S. What has been so amazing is the multiplier effect of this program and its popularity with teachers and alumni alike has resulted in the creation of an active online social media community of G-Camp attendees through Facebook.
In fact, to date G-Camp has positively impacted more than 490,000 students since the program’s inception, estimates Dr. Rick Giardino, professor, Geology & Geophysics, Texas A&M University and G-Camp founder. “Participating teachers consistently rank G-Camp as one of the most impactful professional development programs of their careers,” he said.
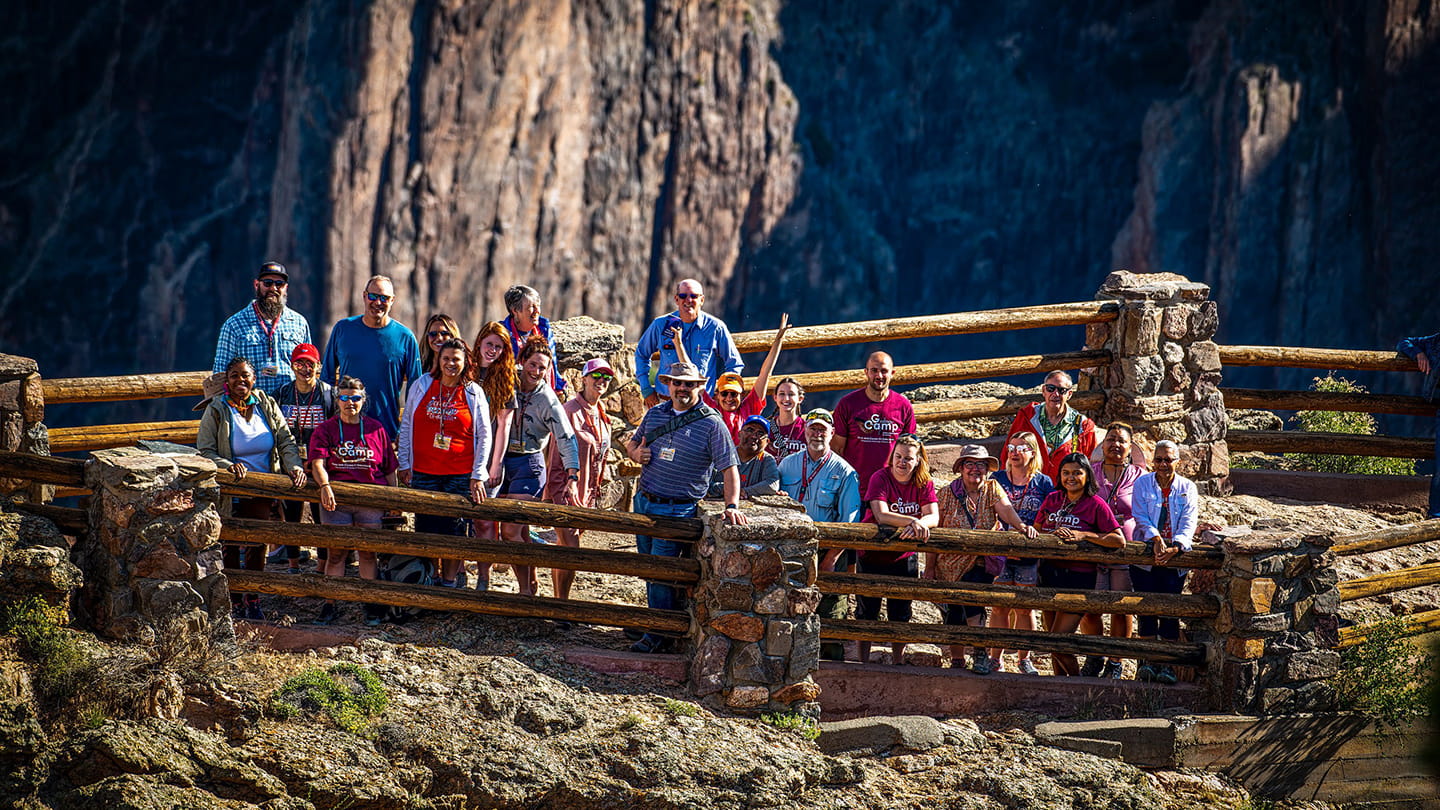
G-Camp class of 2022 taken at Black Canyon of the Gunnison National Park, Colorado, as part of the trek to national parks for field experience and to learn about geologic phenomena and mapping. Along the way teachers gather rock specimens to bring back to the classroom making the learning experience more personal and impactful.